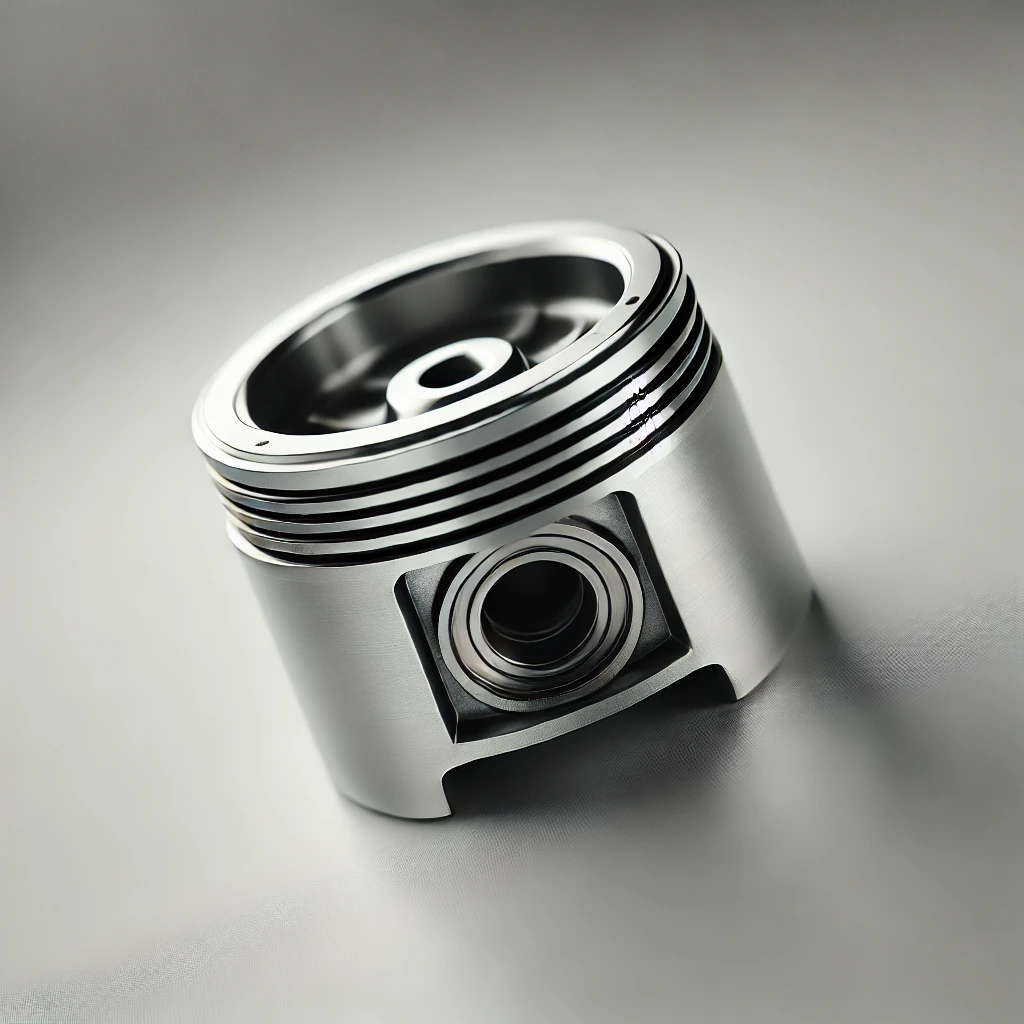
Análise de Componentes Mecânicos
Importância da análise de componentes mecânicos na manutenção industrial
A análise de componentes mecânicos é um pilar fundamental na manutenção industrial, pois permite garantir o funcionamento ótimo das máquinas e prevenir falhas dispendiosas. Num ambiente industrial, onde a eficiência operacional e a redução de custos são cruciais, a análise de componentes mecânicos torna-se uma ferramenta indispensável para a manutenção preditiva e corretiva, ajudando a maximizar a vida útil dos equipamentos e a minimizar o tempo de inatividade.
Um dos principais benefícios da análise de componentes mecânicos na manutenção industrial é a capacidade de detetar problemas antes que se tornem falhas catastróficas. Através de técnicas avançadas como análise de vibrações, termografia, ultrassom e análise de lubrificantes, é possível identificar sinais precoces de desgaste, corrosão, desequilíbrio ou sobreaquecimento nos componentes mecânicos. Estes problemas, se não forem abordados a tempo, podem resultar em avarias imprevistas que interrompem a produção e geram custos elevados em reparações e substituições.
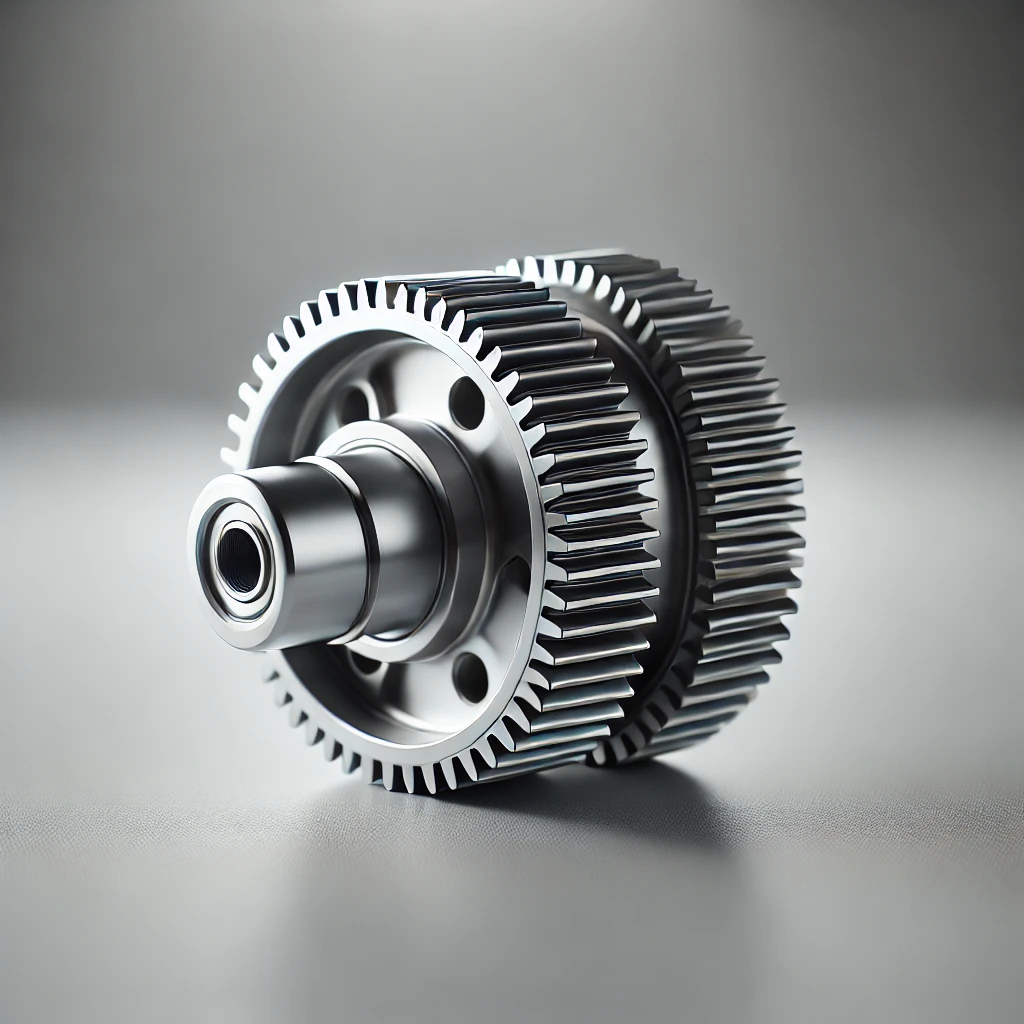
A análise de componentes mecânicos também é essencial para a manutenção preventiva. Em vez de realizar manutenções programadas com base apenas no tempo de operação, a análise permite que engenheiros e técnicos tomem decisões baseadas no estado real dos componentes. Isso não só otimiza o tempo de manutenção, mas também reduz a possibilidade de intervenções desnecessárias que poderiam afetar o desempenho dos equipamentos. Ao implementar uma abordagem de manutenção baseada nas condições, as indústrias podem poupar tempo e recursos, melhorando ao mesmo tempo a fiabilidade das máquinas.
Além disso, a análise de componentes mecânicos desempenha um papel crucial na melhoria da segurança industrial. As falhas nos componentes mecânicos não só podem afetar a produção, como também representam riscos significativos para a segurança dos trabalhadores. Por exemplo, uma falha num rolamento ou numa peça estrutural de uma máquina pesada pode provocar acidentes graves. A análise de componentes mecânicos permite identificar e mitigar esses riscos ao garantir que todos os componentes críticos estão em bom estado e a funcionar dentro dos parâmetros seguros.
Outra vantagem significativa da análise de componentes mecânicos na manutenção industrial é a otimização do desempenho das máquinas. À medida que os componentes mecânicos se desgastam, o desempenho da maquinaria pode ser comprometido, resultando em menor produtividade e maior consumo de energia. Ao realizar análises regulares, é possível ajustar e otimizar os componentes para que funcionem de forma mais eficiente, traduzindo-se em maior produtividade e menores custos operacionais. Isto é especialmente importante em indústrias onde o consumo energético representa uma parte significativa dos custos operacionais.
A análise de componentes mecânicos também é fundamental para prolongar a vida útil dos equipamentos. As máquinas industriais são investimentos dispendiosos, e a sua substituição pode representar um custo considerável para as empresas. Ao monitorizar continuamente o estado dos componentes mecânicos e realizar manutenções oportunas, é possível prolongar a vida útil das máquinas, adiando a necessidade de grandes investimentos em novos equipamentos. Isso não só contribui para a estabilidade financeira da empresa, mas também ajuda a reduzir o impacto ambiental ao minimizar o desperdício de equipamentos em bom estado.
Em resumo, a análise de componentes mecânicos é uma ferramenta essencial na manutenção industrial. Ao permitir a deteção precoce de problemas, otimizar a manutenção preventiva, melhorar a segurança, otimizar o desempenho e prolongar a vida útil dos equipamentos, a análise de componentes mecânicos tornou-se uma parte integrante da estratégia de manutenção nas indústrias modernas. As empresas que investem nestas tecnologias e práticas podem desfrutar de maior eficiência operacional, menores custos e um ambiente de trabalho mais seguro.
Métodos avançados para a análise de componentes mecânicos: Tecnologia e precisão
No âmbito da análise de componentes mecânicos, a tecnologia e a precisão desempenham um papel crucial para garantir que as máquinas e os sistemas industriais funcionem de forma ótima. Com o avanço da engenharia e a introdução de novas tecnologias, os métodos de análise tornaram-se cada vez mais sofisticados, permitindo aos técnicos e especialistas identificar problemas com maior exatidão e em menos tempo. Os métodos avançados para a análise de componentes mecânicos não só ajudam a prevenir falhas, como também otimizam a manutenção preditiva e corretiva.
Um dos métodos mais comuns na análise de componentes mecânicos é a análise de vibrações. Este método baseia-se na medição das vibrações geradas pelos componentes mecânicos, como rolamentos, eixos e motores. Cada componente tem um padrão de vibração específico quando está em bom estado. Qualquer desvio desse padrão pode indicar um problema, como desgaste, desalinhamento, desequilíbrio ou falhas nos rolamentos. A análise de vibrações permite detetar esses problemas numa fase inicial, evitando falhas catastróficas. Graças a sensores avançados e software de análise, os engenheiros podem interpretar estes dados com precisão e tomar decisões informadas sobre a manutenção necessária.

Outro método-chave é a análise de ultrassom, utilizada principalmente para detetar fugas de ar e gás, bem como falhas elétricas e mecânicas nas suas fases iniciais. O ultrassom permite aos técnicos ouvir sons que não são audíveis para o ouvido humano e que podem indicar problemas como cavitação em bombas, fugas de pressão ou mesmo arcos elétricos em sistemas de alta tensão. Na análise de componentes mecânicos, o ultrassom é utilizado para detetar problemas em sistemas hidráulicos, pneumáticos e elétricos. Este método é particularmente valioso, pois pode identificar problemas antes de se manifestarem na forma de falhas graves, permitindo realizar reparações de forma proativa.
A termografia infravermelha é outro método avançado utilizado na análise de componentes mecânicos para detetar problemas relacionados com o calor. Os componentes mecânicos sujeitos a fricção, sobrecarga ou desgaste tendem a gerar calor excessivo. A termografia infravermelha utiliza câmaras especializadas para detetar esses pontos quentes em motores, rolamentos, sistemas elétricos e outros componentes. Ao visualizar a distribuição do calor nos sistemas mecânicos, os engenheiros podem identificar problemas que não seriam visíveis a olho nu, como um sobreaquecimento num rolamento ou um problema de isolamento num sistema elétrico. Este método é altamente preciso e não invasivo, o que o torna uma ferramenta valiosa na manutenção preditiva.
A análise de lubrificantes também é essencial na análise de componentes mecânicos. Este método envolve a amostragem e análise do óleo ou lubrificante utilizado nos sistemas mecânicos. Os lubrificantes contêm informações valiosas sobre o estado dos componentes internos. Por exemplo, a presença de partículas metálicas no lubrificante pode indicar desgaste nos engrenagens ou rolamentos. A análise de lubrificantes permite detetar problemas como contaminação, oxidação e degradação do óleo, o que pode afetar o desempenho e a vida útil dos componentes. Ao realizar análises regulares dos lubrificantes, as empresas podem planear a manutenção de forma mais eficaz e evitar falhas inesperadas.
Finalmente, a inspeção visual automatizada é um método avançado que utiliza câmaras e software de inteligência artificial para realizar inspeções detalhadas de componentes mecânicos. Esta abordagem é usada comumente em linhas de produção para identificar defeitos em peças e montagens. As câmaras de alta resolução capturam imagens detalhadas dos componentes, enquanto o software analisa essas imagens em busca de imperfeições, desgaste ou defeitos. Este método é altamente eficiente e preciso, permitindo aos fabricantes assegurar a qualidade dos seus produtos e componentes antes de entrarem em operação.
Em resumo, os métodos avançados para a análise de componentes mecânicos são essenciais para garantir a fiabilidade e o desempenho dos sistemas industriais. Tecnologias como a análise de vibrações, ultrassom, termografia infravermelha, análise de lubrificantes e inspeção visual automatizada permitem aos engenheiros detetar problemas com precisão e tomar medidas proativas para evitar falhas. Ao incorporar essas tecnologias nas suas estratégias de manutenção, as empresas podem melhorar a eficiência operacional, reduzir os custos de manutenção e prolongar a vida útil dos seus equipamentos.
Como a análise de componentes mecânicos melhora a eficiência na produção
A análise de componentes mecânicos desempenha um papel crucial na otimização da eficiência na produção industrial. Ao garantir que todos os componentes mecânicos das máquinas e sistemas funcionem de forma ótima, as empresas podem maximizar a produtividade, reduzir o tempo de inatividade não planeado e diminuir os custos operacionais. Num ambiente de produção altamente competitivo, onde cada segundo conta, a análise de componentes mecânicos torna-se uma ferramenta essencial para manter os processos produtivos a funcionar sem problemas e com a máxima eficiência.
Uma das formas em que a análise de componentes mecânicos melhora a eficiência na produção é através da deteção precoce de falhas. Os componentes mecânicos, como rolamentos, engrenagens, correias e motores, estão sujeitos a desgaste e fadiga devido ao uso constante. Se estas falhas não forem detetadas a tempo, podem causar avarias que interrompem o processo produtivo. A análise de componentes mecânicos permite aos técnicos identificar problemas iniciais antes que se tornem falhas graves. Usando técnicas como análise de vibrações, termografia infravermelha e análise de lubrificantes, os engenheiros podem monitorizar o estado dos componentes em tempo real e programar a manutenção preventiva, evitando assim paragens não planeadas na linha de produção.

Além disso, a análise de componentes mecânicos permite às empresas adotar uma abordagem de manutenção preditiva em vez de reativa. Tradicionalmente, a manutenção das máquinas era realizada com base num calendário fixo ou após a ocorrência de falhas. No entanto, essa abordagem não é eficiente, pois pode resultar em tempo de inatividade desnecessário ou em reparações dispendiosas. Com a análise de componentes mecânicos, as empresas podem monitorizar o estado real dos componentes e realizar a manutenção apenas quando necessário. Isso não só reduz os custos de manutenção, como também melhora a disponibilidade dos equipamentos e aumenta a produtividade na fábrica.
Outra forma em que a análise de componentes mecânicos melhora a eficiência na produção é otimizando o desempenho das máquinas. Componentes mecânicos em mau estado ou mal ajustados podem afetar o desempenho geral da maquinaria, resultando numa velocidade de produção inferior ou em produtos de menor qualidade. A análise de componentes mecânicos permite aos técnicos identificar problemas que possam estar a afetar o desempenho, como o desgaste dos rolamentos ou a desalinhamento dos eixos, e corrigi-los antes que impactem a produção. Ao assegurar que todos os componentes estão em ótimas condições, as empresas podem melhorar a eficiência das suas linhas de produção e manter altos padrões de qualidade.
Além disso, a análise de componentes mecânicos contribui para a redução dos custos operacionais. Quando os componentes mecânicos funcionam de maneira ótima, as máquinas consomem menos energia e operam de forma mais eficiente. Problemas mecânicos não detetados, como desgaste excessivo ou fricção desnecessária, podem aumentar o consumo de energia e provocar maior desgaste nas peças, o que, por sua vez, aumenta os custos de operação. Ao realizar análises regulares e corrigir os problemas a tempo, as empresas podem reduzir os seus custos de energia e minimizar a necessidade de reparações ou substituições de equipamentos dispendiosas.
Finalmente, a análise de componentes mecânicos melhora a eficiência na produção ao prolongar a vida útil das máquinas. As máquinas industriais são investimentos significativos, e a substituição frequente de equipamentos pode afetar gravemente os orçamentos operacionais. A manutenção adequada, baseada na análise detalhada dos componentes mecânicos, permite às empresas estender a vida útil dos seus ativos. Isto não só reduz os custos de capital, como também assegura que a produção possa continuar sem interrupções significativas durante mais tempo.
Em resumo, a análise de componentes mecânicos é uma ferramenta poderosa para melhorar a eficiência na produção industrial. Ao permitir a deteção precoce de falhas, otimizar a manutenção preditiva, melhorar o desempenho das máquinas, reduzir os custos operacionais e prolongar a vida útil dos equipamentos, este tipo de análise contribui significativamente para a produtividade e rentabilidade das operações industriais. As empresas que integram a análise de componentes mecânicos nas suas estratégias de manutenção e produção estão melhor posicionadas para competir num mercado cada vez mais exigente.
Casos de sucesso na indústria: Benefícios da análise de componentes mecânicos
A análise de componentes mecânicos tem-se mostrado uma ferramenta essencial para melhorar a eficiência, segurança e rentabilidade em várias indústrias. Graças à implementação de tecnologias avançadas e uma abordagem proativa na manutenção, muitas empresas têm experimentado melhorias significativas nas suas operações. Neste artigo, exploramos alguns casos de sucesso na indústria e os benefícios tangíveis que a análise de componentes mecânicos trouxe para estas organizações.
*Caso 1: Indústria Automotiva*
Na indústria automotiva, onde a produção em massa e a eficiência operacional são primordiais, uma empresa fabricante de automóveis líder decidiu implementar um programa abrangente de análise de componentes mecânicos nas suas plantas de montagem. Anteriormente, a empresa enfrentava frequentes interrupções na produção devido a falhas inesperadas nos componentes das suas linhas de montagem automatizadas. Estas falhas resultavam em períodos de inatividade dispendiosos e afetavam a capacidade da empresa de cumprir os prazos de entrega.
Com a introdução da análise de componentes mecânicos, a empresa pôde monitorizar de perto o estado dos rolamentos, motores e sistemas de transmissão nas suas linhas de montagem. Usando técnicas como análise de vibrações e termografia infravermelha, os engenheiros identificaram problemas nas suas fases iniciais, permitindo realizar a manutenção preventiva antes que ocorressem falhas graves. Como resultado, a empresa reduziu o tempo de inatividade em 30% e aumentou a eficiência de produção em 20%. Além disso, a análise também ajudou a reduzir os custos de manutenção e prolongou a vida útil dos equipamentos, resultando numa economia significativa a longo prazo.
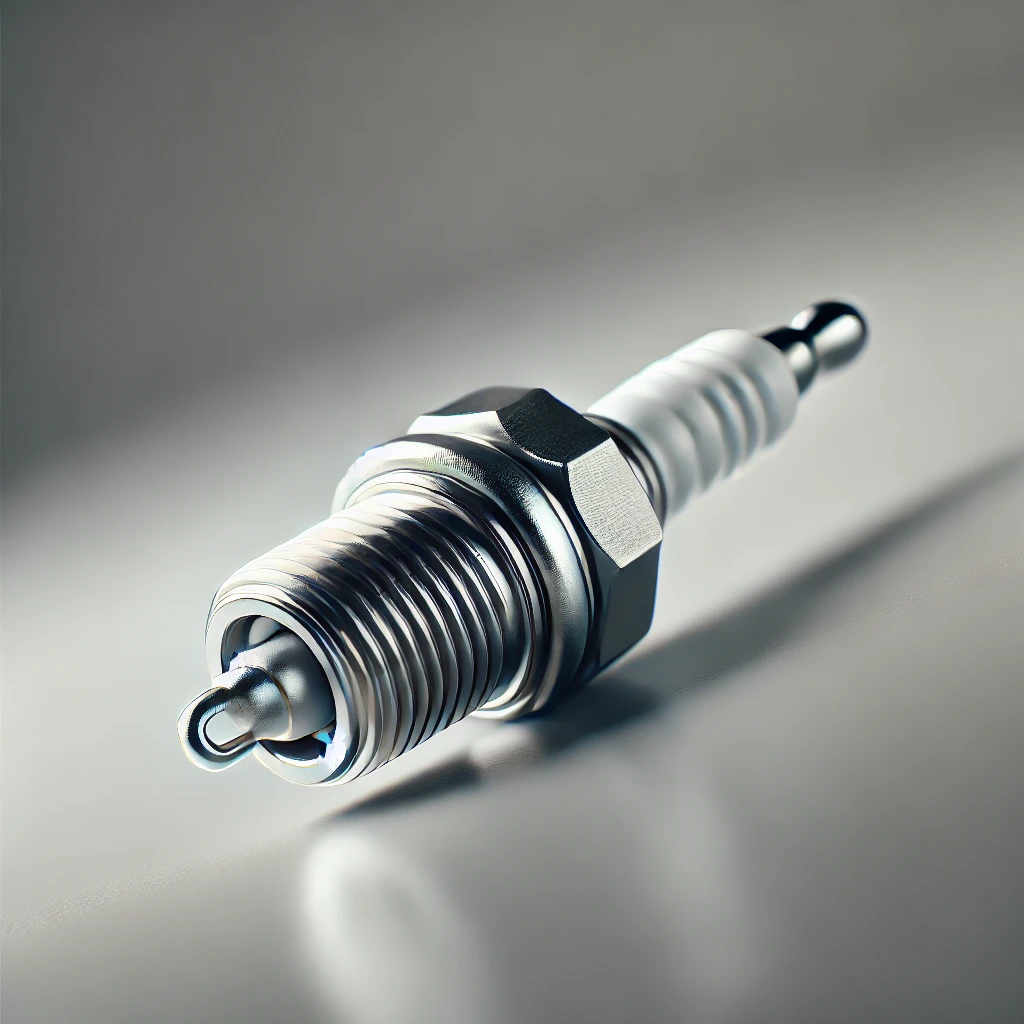
Caso 2: Indústria Energética*
Na indústria energética, onde a fiabilidade dos equipamentos é fundamental para garantir um fornecimento contínuo de eletricidade, uma empresa de geração de energia implementou a análise de componentes mecânicos nas suas turbinas e geradores. Anteriormente, a empresa enfrentava falhas recorrentes nos seus sistemas de geração devido ao desgaste de componentes críticos, o que provocava cortes de energia e elevados custos de reparação.
Com o uso da análise de componentes mecânicos, a empresa conseguiu monitorizar constantemente o estado das suas turbinas e geradores. A análise de ultrassom permitiu detetar microfissuras e desgaste nos rolamentos, enquanto a análise de lubrificantes identificou problemas de contaminação e oxidação nos sistemas de lubrificação. Com estas informações, a empresa pôde realizar ajustes e reparações de forma proativa, evitando falhas catastróficas. Como resultado, a empresa melhorou a fiabilidade dos seus equipamentos e reduziu os custos operacionais em 25%. Além disso, a análise permitiu à empresa cumprir com os rigorosos padrões de segurança e ambientais, melhorando a sua reputação no setor.
Caso 3: Indústria de Alimentos e Bebidas*
Na indústria de alimentos e bebidas, onde a qualidade do produto e a eficiência na produção são fatores críticos, uma fábrica de processamento de alimentos decidiu integrar a análise de componentes mecânicos nas suas linhas de produção. A fábrica enfrentava problemas recorrentes com os motores e correias transportadoras na sua linha de processamento, o que afetava a consistência e qualidade do produto final.
A análise de componentes mecânicos permitiu à fábrica identificar problemas como o sobreaquecimento dos motores e o desgaste dos rolamentos antes que afetassem a produção. Utilizando a análise de vibrações e a inspeção visual automatizada, a fábrica fez ajustes nos sistemas mecânicos e otimizou a sua manutenção. Como resultado, a fábrica melhorou a consistência do produto e reduziu o desperdício em 15%. Além disso, ao reduzir as interrupções na produção, a fábrica aumentou a sua capacidade de produção em 10%, permitindo atender à crescente procura do mercado.
Estes casos de sucesso demonstram como a análise de componentes mecânicos pode transformar as operações em várias indústrias. Ao implementar esta abordagem proativa, as empresas têm experimentado melhorias significativas na eficiência, qualidade do produto e rentabilidade. Os benefícios da análise de componentes mecânicos são claros: redução do tempo de inatividade, diminuição dos custos de manutenção, prolongamento da vida útil dos equipamentos e melhoria da fiabilidade operacional. Estas vantagens posicionam as empresas para competir com maior eficácia nos seus mercados, garantindo ao mesmo tempo um desempenho ótimo dos seus sistemas e máquinas.